In this blog I will share everything about proximity sensors. What is proximity sensors, where it should be used and what is the difference between each sensors, all its types. So it such as capacitive proximity sensor, inductive proximity sensor and ultrasonic proximity sensor are used to detect the presence of objects nearby. These are used for object positioning and proximity based automation. Proximity sensors are usually non-contact, meaning they do not require physical contact. Like other sensors, they have a specific detection range to detect the presence of objects nearby. When an object comes within the dictation range of the proximity sensor, the sensor is triggered and a signal is generated as well. This signal is then used for object detection distance measurement.
Table of Contents
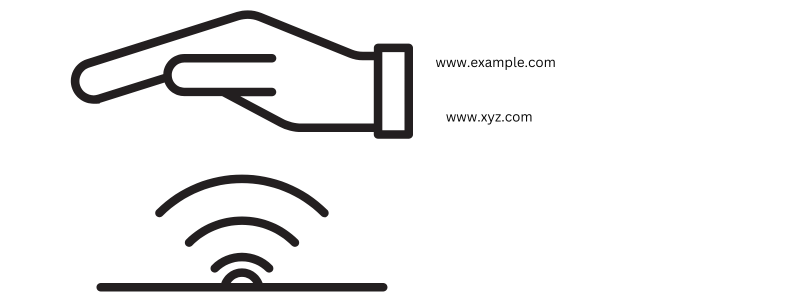
1. CAPACITIVE PROXIMITY SENSORS
It uses the electrical properties to detect the presence of near by object.Capacitive sensors are used to detect the presence of nearby objects by using the electrical properties. These sensors are used to measure dielectric constant and electrical conductivity based variations. Proximity sensors are primarily non-contact, meaning they do not require physical contact with the object. Capacitive proximity sensors typically have two electrical conductors or electrodes separated by a dielectric material, i.e. a non-conductive material. When an object such as an insulator or conductor interacts with the electromagnetic field of a capacitive proximity sensor, variations in the electromagnetic field are produced. These variations are detected by the sensor, and the sensor determines how close the object is. Capacitive proximity sensors have several features and characteristics, such as the detection range, object type, sensitivity adjustment and environmental factors.
DETECTION RANGE:
The deduction range of a capacitive sensor is generally short, typically it can be up to a few MM to few CM. In this range, the sensor can detect objects. This is a given range, as every sensor has some range.
OBJECT TYPE :
Capacitive proximity sensors can usually detect both non-metallic and metallic objects. The detection range of metal objects is usually less than that of non-metallic objects.
SENSETIVITY ADJUSTMENT :
Some capacitive sensors have the facility to adjust the sensitivity, which means we can adjust them so that they can be customized for specific applications.
ENVIRONMETAL FACTORS :
Capacitive sensors are sensitive to environmental factors such as temperature, humidity and dust particles, so it becomes important to use them in suitable operating conditions.
APPLICATIONS :
Capacitive Proximity sensors are used in object detection, liquid level sensing, touch sensitivity interfaces, and proximity-based automation applications. These sensors are widely used in industrial automation, consumer electronics, mobile app devices, and the automotive industry.
2. INDUCTIVE PROXIMITIY SENSOR
Inductive proximity sensor are used to detect the presence of metallic objects. These sensors use the principle of electromagnetic induction, i.e., inductive proximity sensors work on electromagnetic induction. In an inductive proximity sensor, there is generally a coil, which we call primary coil or transmitter coil. In this coil, there is an alternating current, i.e., a flow, due to which an electromagnetic field is generated in the coil. When a metallic object enters the electromagnetic field of the proximity sensor, its magnetic field lines interact with the sensor. This interaction generates a secondary electromagnetic field which creates electromagnetic induction in the primary coil. This induction results in change in voltage and current in the primary coil. Inductive proximity sensor detects the variation in voltage and current of the primary coil. When a metallic object is in the deduction range of the sensor, changes in electromagnetic induction are detected in the sensor. These are detectable in electrical circuits and trigger a signal. When the sensor is triggered, a corresponding signal is generated in the output circuit. This signal is then used for object detection, position counting and automation tasks. Inductive proximity sensors can detect primary metallic objects such as ferrous metals because metals have magnetic properties. These sensors are non-contact, meaning they do not require physical contact with the object. The detection range, sensitivity and operating conditions, frequency, voltage and current of these sensors can vary according to the model and also depend on the manufacturer. Inductive proximity sensors generally have 3 types of components.
Oscillator:
This component generates an alternating current inside the sensor, called an oscillator. The frequency of this oscillator is typically high. Some may have a lower frequency.
Coil :
This coil receives the alternating current generated by the oscillator. The coil generates an electromagnetic field that extends beyond the front face of the sensor.
Metal Target :
If any metallic object comes within the electromagnetic field of the sensor, then the electromagnetic field effect occurs.
Application :
We use inductive proximity sensors a lot in industrial automation, robotic machine monitoring and object detection applications.
also you should know about charging system of ev.
3. ULTRASONIC PROXIMITY SENSOR
Ultrasonic sensor is a sensor that is used to detect the presence and distance of objects using ultrasonic sound waves. This sensor generates sound waves and calculates the distance of the object by receiving their echo. An ultrasonic proximity sensor has some major components such as
Transmitter :
This component generates ultrasonic sound waves. It generates ultrasonic sound waves. It usually uses piezoelectric crystals that convert electric voltage into mechanical vibrations and emit sound waves.
Receiver:
This component receives the echo of the ultrasonic sound wave. The sound waves sent out by a transmitter bounce back . When the ultrasonic sensor releases any sound wave, that sound wave hits any object in front of it and comes back and after coming back the receiver detects it.
Timing And Control Circuit :
This circuit controls the sound and reception. It involves time delay and pulse generation. We will talk about it later. Ultrasonic proximity sensor emits sound waves and then these sound waves bounce back after colliding with the surrounding object. These bounced back sound waves are detected by the receiver of the sensor. The timing and control circuit measures the time delay of these echo sound waves. The distance of the sensor from the object is calculated from the time delay. The calculation of the sensor depends on the principles as called time of flight or doffer effect principle. In what way, how much distance has the sound wave emitted by the ultrasonic sensor travelled? In time and flight principles, the time delay between emission and reception of the sound wave represents the distance. In doffer effect principles, any change in the frequency of the sound wave can be calculated from the motion of the object. Ultrasonic proximity sensors can detect the presence and distance of nearby objects.
Application :
Ultrasonic Proximity Sesnors are used in industrial automation, robotics and parking assistance.
http://neverhood.etomite.sk/online/post/10543/#p10543
https://ufo.hosting/
https://the.hosting/pt/help/verificacao-do-alojamento-de-dominios
https://the.hosting/et/help/kuidas-salvestada-faili-nano-linuxis